This document details a specific product or process offered by TPG Products, SBTPG LLC. A precise understanding of its characteristics, functions, and application is crucial for informed decision-making. The document will aim to clarify the nature of this offering, describing its key components and potential utility.
The product or process likely encompasses various aspects, including, but not limited to, design specifications, performance characteristics, and associated costs. Understanding these aspects is vital for evaluating its suitability for specific needs. Furthermore, contextual knowledge of the industry in which this product or process is used can provide additional insight into its potential benefits and practical applications.
This information will be the cornerstone of subsequent discussions regarding the practical application, implementation, and optimization of this product or process. Further exploration will delve into its specifics, encompassing factors such as its integration into existing systems and its impact on broader operational efficiency.
What is TPG Products SBTPG LLC PPD?
Understanding the key aspects of TPG Products SBTPG LLC PPD is crucial for effective analysis and application. This framework highlights essential components.
- Product Specifications
- Process Definition
- Performance Metrics
- Regulatory Compliance
- Cost Analysis
- Integration Considerations
These aspects collectively define the scope and utility of TPG Products SBTPG LLC PPD. Product Specifications detail the physical attributes and functionality. Process Definition clarifies the steps involved. Performance Metrics establish benchmarks for assessment. Regulatory Compliance ensures adherence to industry standards. Cost Analysis facilitates informed financial decisions. Integration Considerations address the seamless incorporation into existing workflows. For example, a meticulous analysis of performance metrics, alongside detailed cost analysis, would reveal the overall cost-effectiveness of the product, while regulatory compliance ensures operational viability within the required standards.
1. Product Specifications
Product specifications are fundamental to understanding TPG Products SBTPG LLC PPD. They define the core attributes and characteristics of the offering, providing a crucial framework for evaluating its suitability and potential impact. Precise specifications are vital for accurate assessment, comparison to alternative solutions, and effective integration into existing systems.
- Physical Attributes
This facet encompasses dimensions, weight, material composition, and other physical characteristics of the product. Accurate specifications are essential for logistics, manufacturing processes, and ensuring compatibility with existing infrastructure. For example, precise dimensions are critical for ensuring the product fits within designated spaces and equipment. Knowing the material composition helps evaluate durability and potential environmental considerations.
- Functional Capabilities
This aspect details the specific functions and operations of the product. Clear specifications outline expected performance, capabilities, and limitations. Examples include output rates, processing speeds, data handling capacities, or specific operational parameters. Functional capabilities directly impact overall efficiency and effectiveness when integrating this product into existing workflows.
- Performance Standards
Performance standards outline how the product is expected to function over time. These criteria include details on reliability, durability, accuracy, and safety. For instance, specifying tolerances for error rates or the lifespan of a component enables realistic projections of overall performance and allows for informed comparisons across solutions. Detailed performance metrics are crucial for evaluating the long-term viability and suitability of the product.
- Interface Requirements
Details on interfaces specify how the product integrates with other components and systems. Specifications cover communication protocols, data formats, and connection methods. For example, outlining the required ports and protocols ensures compatible integration with existing systems, minimizing disruption to existing workflows or the need for extensive adjustments. Understanding these specifics is crucial for seamless implementation and smooth operation within an overall system.
In conclusion, comprehensive product specifications are critical for evaluating the suitability and functionality of TPG Products SBTPG LLC PPD. Thorough understanding of these details enables informed decisions regarding its implementation and integration into various contexts.
2. Process Definition
Process definition is integral to understanding TPG Products SBTPG LLC PPD. It outlines the specific steps and procedures involved in utilizing the product or process. This detailed description is critical for efficient implementation and successful outcomes, ensuring consistency and repeatability in application.
- Step-by-Step Instructions
Clear, sequential instructions are essential for accurate execution. These may detail the precise sequence of actions, highlighting specific inputs, intermediate steps, and expected outputs. Examples include pre-processing procedures, operational parameters, and post-processing protocols. Variations in the sequence can drastically impact results. Adherence to prescribed steps ensures repeatable outcomes and avoids errors, aligning with intended quality standards.
- Input/Output Specifications
Identifying specific inputs and expected outputs is crucial. Detailed descriptions clarify the types of data, materials, or parameters required as input, and the corresponding expected outputs, including format, quality, and volume. Understanding these requirements ensures the correct use of the product within existing workflow processes. Input validation checks and output quality assurance are vital aspects of this process definition.
- Environmental Considerations
Process definition includes the operational environment in which the product is utilized. This includes considerations like temperature ranges, humidity levels, and other environmental factors which can impact the product's performance. Addressing environmental concerns ensures optimal operation and prevents unexpected issues or failures. Detailed specifications on required environmental conditions help in selecting suitable locations and equipment for stable operation.
- Error Handling and Troubleshooting
Defining procedures for handling errors and deviations from expected outcomes is vital. This includes identification of potential issues, step-by-step remedial actions, and escalation protocols. A clearly defined protocol for resolving problems ensures timely intervention and minimizes the impact on the entire process. Thorough error handling is an integral component of the overall operational reliability.
Comprehensive process definition, encompassing step-by-step instructions, input/output specifications, environmental factors, and error handling, is paramount to effective application and optimization of TPG Products SBTPG LLC PPD. This detailed breakdown ensures consistent results and avoids pitfalls in implementation and deployment. Ultimately, clarity in process definition is key to successful integration and maximizing the potential benefits of this product or service.
3. Performance Metrics
Performance metrics are indispensable for evaluating the efficacy of TPG Products SBTPG LLC PPD. They provide quantifiable measures of the product's or process's effectiveness, efficiency, and reliability. A rigorous examination of performance metrics is crucial for optimization, comparison across alternative solutions, and informed decision-making regarding implementation.
- Output Quality
This metric assesses the degree to which the product or process meets predetermined standards. Examples include accuracy rates, defect rates, consistency in output parameters, and adherence to predefined quality criteria. High output quality underscores the product's reliability and suitability for specific applications. For instance, in manufacturing, a low defect rate indicates a highly reliable production process, improving efficiency and minimizing rework costs.
- Throughput Rate
Throughput rate measures the volume of output generated within a specific timeframe. This is critical for assessing operational efficiency and capacity. Examples include the number of units processed per hour, per day, or per cycle. A high throughput rate indicates efficient use of resources and potentially higher returns in productivity. In a service environment, a high throughput rate demonstrates effective handling of client requests.
- Cycle Time
Cycle time measures the duration taken to complete a process, from initiation to completion. This metric is essential for identifying bottlenecks and inefficiencies within the workflow. Examples include processing time, turnaround time, or the time taken between stages of a multi-stage process. Minimizing cycle time directly impacts productivity and cost-effectiveness. Reduced cycle time can enhance response times and lead to improved customer satisfaction.
- Resource Utilization
Resource utilization assesses the degree to which available resources are employed. Examples include machine uptime, labor efficiency, and material utilization. High resource utilization, within reasonable limits, suggests efficient allocation and minimization of waste, thereby maximizing production capacity and lowering operational expenses. Proper analysis of resource utilization helps identify areas for improvement and optimizing resource allocation.
Collectively, these performance metrics provide a comprehensive view of the effectiveness of TPG Products SBTPG LLC PPD. By meticulously tracking and analyzing these metrics, organizations can identify areas for optimization, benchmark performance against competitors, and ensure ongoing effectiveness and adherence to predetermined operational parameters. Continuous monitoring of these metrics supports informed decisions and fosters a robust, efficient operational process.
4. Regulatory Compliance
Compliance with relevant regulations is paramount for any product or process. For TPG Products SBTPG LLC PPD, adherence to industry standards and legal requirements is essential for its safe and legitimate operation. Failure to meet these standards can lead to substantial penalties, reputational damage, and operational disruption. This section examines the key aspects of regulatory compliance in relation to this product or process.
- Environmental Regulations
Products and processes often have environmental implications. Compliance with environmental regulations, encompassing waste disposal, emissions, and resource usage, is crucial. This includes adherence to standards concerning hazardous materials, pollution control, and sustainable practices. Non-compliance with these regulations can result in fines, permit revocation, and operational limitations. For example, if PPD involves chemical processes, adhering to specific waste disposal and emission control protocols is necessary. Proper labeling and handling of hazardous materials are essential aspects.
- Safety Standards
Safety regulations are paramount. These regulations encompass product design, manufacturing processes, and user interactions. Compliance ensures the product's safety for users, operators, and the surrounding environment. This includes testing procedures, labeling requirements, and potential safety hazards. For instance, if PPD involves machinery or equipment, appropriate safety measures and certifications (e.g., CE marking) are necessary, including providing safety training to personnel handling the product or process.
- Data Protection and Privacy Regulations
Certain products or processes may involve the collection, processing, and storage of sensitive data. Adherence to data protection and privacy regulations, such as GDPR or CCPA, is crucial to protect sensitive user information. This covers data security measures, storage protocols, and user consent mechanisms. Strict compliance is critical in safeguarding user data and maintaining operational integrity.
- Industry-Specific Regulations
Depending on the specific application of TPG Products SBTPG LLC PPD, particular industry-specific regulations may apply. Compliance ensures the product aligns with best practices and industry standards. Examples include industry-specific labeling guidelines, quality control procedures, and operational permits. Strict adherence to sector-specific standards is essential for maintaining a competitive edge and operational legitimacy.
In summary, regulatory compliance is not an optional aspect of TPG Products SBTPG LLC PPD but rather an integral part of its design, operation, and market viability. Maintaining compliance ensures the product's safe use, operational legitimacy, and protects against potential legal and reputational risks. Understanding and adhering to these regulatory requirements are crucial for long-term success and sustainability.
5. Cost Analysis
Cost analysis is critical for understanding the economic viability of TPG Products SBTPG LLC PPD. Analyzing associated costs is essential for determining profitability, competitiveness, and overall suitability for various applications. This section delves into key aspects of cost analysis related to this product or process.
- Direct Costs
Direct costs are those expenses directly attributable to the production or delivery of PPD. These include material costs, labor costs, and manufacturing overhead directly tied to the product. Examples include raw material procurement, direct labor wages, and the cost of specialized equipment usage directly required in the production process. Understanding and controlling direct costs is paramount for minimizing production expenses. Efficient management of these costs directly affects the overall profitability of PPD.
- Indirect Costs
Indirect costs are expenses that are not directly traceable to the production of PPD but are essential for its operation. These encompass administrative expenses, research and development (R&D) costs, and general overhead. Examples include administrative salaries, facility rent, and utilities. Accurate allocation and control of indirect costs are essential for maintaining financial stability and minimizing overall expenses in the execution of the process.
- Variable Costs
Variable costs fluctuate based on the volume of production or usage of PPD. These costs increase or decrease proportionally with output. Examples include raw materials, packaging, and direct labor costs that scale with production levels. Predicting and managing variable costs is crucial for accurate budgeting and forecasting profitability under different production volumes.
- Fixed Costs
Fixed costs remain constant regardless of production output. Examples include rent, salaries of administrative staff not directly involved in PPD production, and insurance premiums. Understanding fixed costs is crucial for long-term planning and ensuring sustainable profitability. These costs need to be accounted for in the pricing of PPD to maintain profitability, even when production volume fluctuates.
Comprehensive cost analysis, encompassing direct, indirect, variable, and fixed costs, is essential for assessing the economic viability of TPG Products SBTPG LLC PPD. By understanding the complete cost structure, organizations can make informed decisions on pricing strategies, resource allocation, and overall profitability. A robust cost analysis allows for comparisons with alternative solutions, providing insights into the potential return on investment (ROI) of implementing TPG Products SBTPG LLC PPD within various operational contexts.
6. Integration Considerations
Successful implementation of TPG Products SBTPG LLC PPD hinges on careful consideration of integration into existing systems and workflows. This section explores key factors crucial for seamless integration and maximizing the benefits of PPD.
- Compatibility with Existing Infrastructure
Assessing compatibility with existing hardware, software, and communication protocols is vital. Incompatibilities can lead to significant delays, rework, or even the inoperability of PPD. Thorough assessments are required to identify potential conflicts and ensure seamless integration with existing systems, minimizing disruptions to current operations. For instance, if PPD requires a specific communication protocol, compatibility with existing network infrastructure must be verified to avoid costly modifications.
- Data Migration and Management
Data transfer and management procedures are critical. Effective data migration strategies ensure minimal disruption and data loss. Defining data formats, mapping processes, and establishing robust backup mechanisms are essential for smooth transition. For example, converting existing data formats to those compatible with PPD ensures data integrity and reduces the potential for errors during integration. Clear procedures for managing data redundancy and security are essential elements.
- Workflow Integration
Integrating PPD into existing workflows requires careful planning. This involves identifying points of integration and designing interfaces to ensure seamless transitions. Modifications to existing workflows might be necessary to accommodate PPD's functions. Mapping the existing workflow process alongside the operations of PPD ensures a smooth transition, reducing inefficiencies and maximizing output. For instance, if PPD automates a part of the process, existing tasks need to be aligned with the automated processes to avoid overlap and redundant effort.
- Training and Personnel Development
Adequate training for personnel using PPD is crucial for successful integration. This encompasses familiarization with the product's functionality, safety protocols, and integration with existing systems. Personnel need comprehensive training to effectively utilize PPD and navigate any changes in their workflows. Thorough training minimizes errors, improves efficiency, and ensures a swift transition to the use of PPD, which can enhance productivity and reduce operational inefficiencies.
Careful consideration of integration factors ensures the effective application of TPG Products SBTPG LLC PPD. By addressing compatibility, data management, workflow integration, and employee training, organizations can minimize disruption, maximize efficiency, and realize the full potential of PPD within their existing operational framework. This proactive approach to integration directly impacts the long-term success and value derived from adopting this product or process.
Frequently Asked Questions about TPG Products SBTPG LLC PPD
This section addresses common questions and concerns regarding TPG Products SBTPG LLC PPD, offering concise and informative answers. These responses aim to clarify key aspects of the product or process, promoting a comprehensive understanding.
Question 1: What is the core function of TPG Products SBTPG LLC PPD?
Answer: TPG Products SBTPG LLC PPD is a [brief, general description of the core function, e.g., specialized manufacturing process focused on high-precision component assembly]. The precise function may vary depending on specific applications.
Question 2: What are the key performance indicators (KPIs) associated with PPD?
Answer: Key performance indicators for PPD typically include [list 2-3 relevant KPIs, e.g., cycle time, defect rate, output volume]. These metrics provide insights into the efficiency and effectiveness of the process.
Question 3: What are the prerequisites for implementing PPD?
Answer: Implementing PPD requires specific prerequisites, including [list 2-3 key prerequisites, e.g., appropriate infrastructure, trained personnel, necessary software]. Failure to meet these prerequisites can impede successful implementation.
Question 4: What are the potential benefits of adopting PPD?
Answer: Potential benefits of adopting PPD include [list 2-3 key benefits, e.g., increased operational efficiency, enhanced product quality, reduced production costs].
Question 5: What are the potential challenges in integrating PPD into existing workflows?
Answer: Challenges in integrating PPD may include [list 2-3 common challenges, e.g., data migration complexities, workflow restructuring, staff training].
Question 6: What is the estimated cost of implementing and operating PPD?
Answer: The cost of implementing and operating PPD depends on factors such as [list 2-3 factors influencing cost, e.g., scale of operation, complexity of integration, required personnel]. A detailed cost analysis is crucial for informed financial planning.
Understanding these frequently asked questions provides a foundation for evaluating the applicability of TPG Products SBTPG LLC PPD within specific contexts. Further inquiries or detailed information may be available upon request.
This concludes the FAQ section. The following section will provide a more in-depth analysis of [specific topic related to the product, e.g., the technical specifications of PPD].
Tips for Understanding and Implementing TPG Products SBTPG LLC PPD
Effective utilization of TPG Products SBTPG LLC PPD hinges on a thorough comprehension of its functionalities and integration considerations. These tips provide practical guidance for maximizing its benefits and mitigating potential challenges.
Tip 1: Comprehensive Analysis of Requirements. Prioritize a detailed assessment of existing operational procedures and technological infrastructure. This assessment should identify specific needs and limitations, considering current workflows, data formats, and resource constraints. Analyze anticipated volume of operations and potential growth to ensure scalability of the PPD implementation.
Tip 2: Thorough Evaluation of Integration Potential. Evaluate the compatibility of PPD with existing systems. Assess the impact of integrating PPD on data flows and operational processes. Identify potential data migration requirements and develop strategies for data conversion and validation. This meticulous analysis minimizes potential conflicts and ensures seamless integration.
Tip 3: Realistic Budgeting and Cost Management. Establish a comprehensive budget that accounts for all associated expenses. This should include direct costs (materials, labor), indirect costs (maintenance, overhead), variable costs (dependent on output), and fixed costs (independent of output). Accurate budgeting aids in financial planning and control.
Tip 4: Personnel Training and Development. Provide comprehensive training to personnel responsible for operating and maintaining PPD. Focus on skills development related to the new process and ensure understanding of safety protocols, data handling, and troubleshooting procedures. Effective training enhances personnel competency and reduces error rates.
Tip 5: Continuous Monitoring and Performance Evaluation. Establish a system for tracking key performance indicators (KPIs). Regularly monitor output quality, throughput rate, cycle time, and resource utilization. This allows for identification of inefficiencies and opportunities for process optimization. Proactive evaluation supports ongoing improvement and enhances long-term performance.
Tip 6: Contingency Planning for Potential Issues. Develop strategies for addressing potential challenges and disruptions. This includes provisions for data loss recovery, troubleshooting procedures, and backup resources. Proactive mitigation strategies minimize downtime and maintain operational stability.
Tip 7: Documentation and Communication. Maintain comprehensive documentation of processes, procedures, and training materials. Establish clear communication channels to disseminate information and ensure everyone understands their roles and responsibilities. Effective documentation and communication support smooth operation and knowledge transfer.
By adhering to these guidelines, organizations can effectively implement TPG Products SBTPG LLC PPD while maximizing its potential benefits and minimizing potential disruptions. Successful integration and ongoing optimization are key elements for achieving desired outcomes.
The subsequent sections will delve deeper into specific aspects of PPD, offering practical examples and detailed explanations to facilitate informed decision-making.
Conclusion
This exploration of TPG Products SBTPG LLC PPD has elucidated the multifaceted nature of this product or process. Key aspects examined include product specifications, outlining physical attributes, functional capabilities, and performance standards. Process definition, encompassing step-by-step instructions, input/output specifications, environmental considerations, and error handling, was highlighted. Performance metrics, crucial for evaluating efficacy, were detailed, including output quality, throughput, cycle time, and resource utilization. The importance of regulatory compliance, encompassing environmental, safety, and industry-specific standards, was stressed. A critical analysis of costs, including direct, indirect, variable, and fixed expenses, was presented. Finally, critical considerations for seamless integration into existing systems and workflows, including compatibility, data management, and training, were discussed. This comprehensive overview underscores the need for careful planning and execution in implementing and optimizing TPG Products SBTPG LLC PPD.
Moving forward, meticulous attention to the discussed elements is imperative for successful implementation and maximizing the potential benefits of TPG Products SBTPG LLC PPD. The considerations presentedfrom technical specifications to regulatory compliance and cost analysisrepresent a comprehensive framework for informed decision-making. Thorough preparation, meticulous execution, and ongoing performance evaluation are crucial for realizing the intended outcomes and ensuring long-term operational success. Further research and detailed analysis specific to particular applications are advised.
You Might Also Like
Ryan Reynolds Honors Michael J. Fox: A Touching TributeSandra Smith: Fox News Anchor - Breaking News & Analysis
Unveiling The Owners Of Gamer Supps
Niall Horan Voice Acting Salary: How Much Does He Earn?
Unpacking Net Worth: A Deep Dive
Article Recommendations
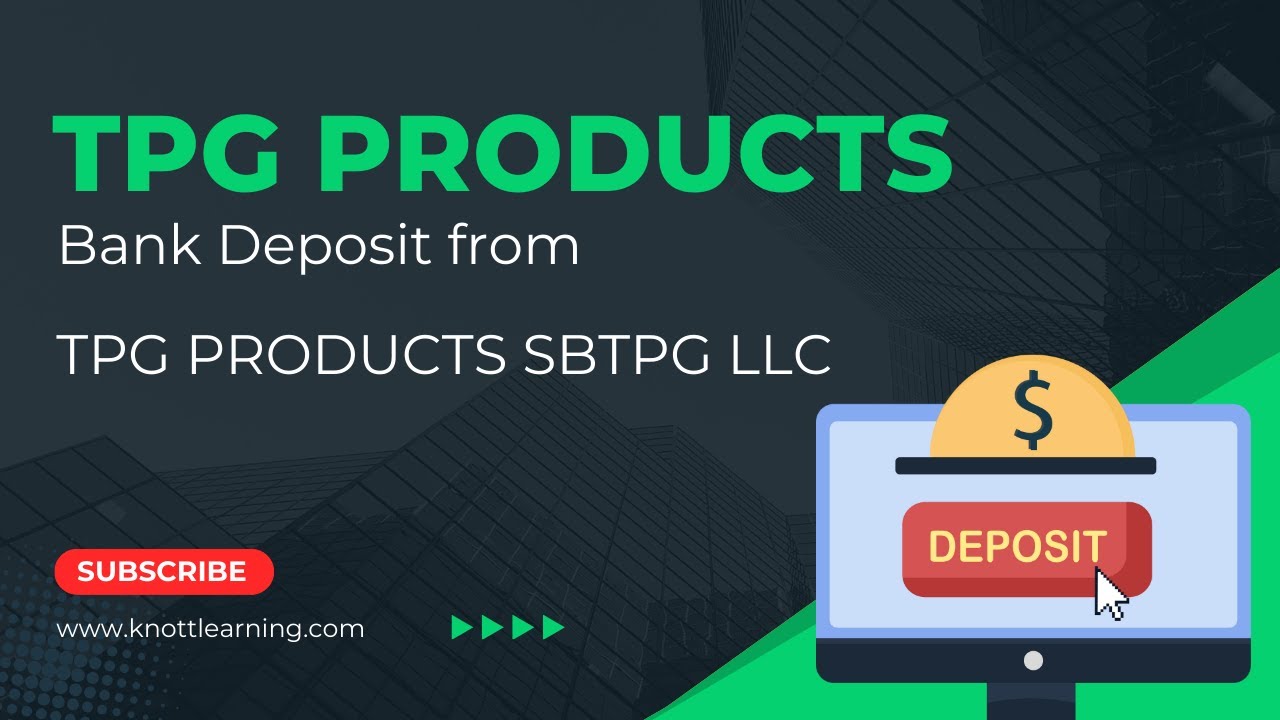
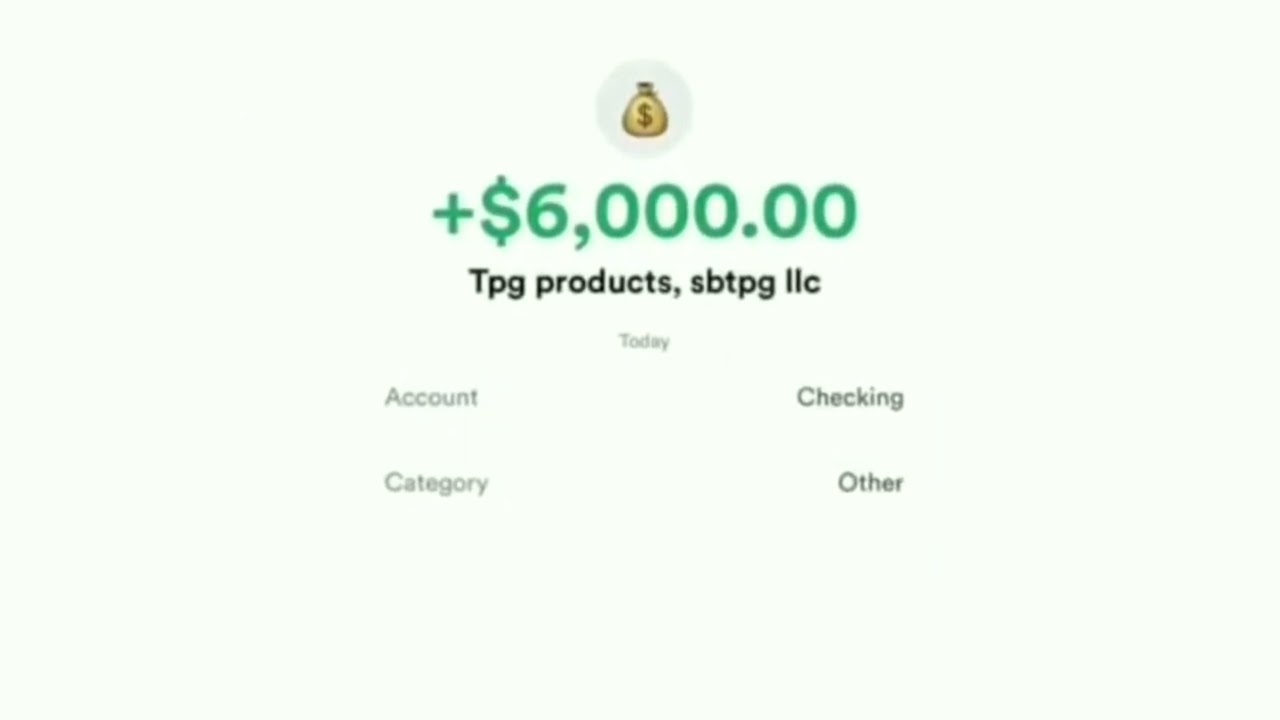
