This term, often used in the context of certain electrical systems, likely refers to a specific type of high-temperature electrical component or a system designed for high-temperature operation. Precise meaning depends on the specific industry or application. Examples might include high-current electrical connectors, specialized heating elements, or electrical systems designed for use in demanding environments with elevated operating temperatures. Understanding the context is crucial for accurate interpretation.
The significance of components designed for high-temperature operation resides in their ability to withstand extreme conditions. This is essential for reliable performance in applications where such temperatures are inherent or required, such as specialized industrial processes, high-performance machinery, or advanced research environments. Historical development of these components has likely focused on materials science and engineering solutions to meet increasing operational demands. Successful implementation of these technologies leads to increased efficiency and longevity of critical systems.
Further discussion of this concept would benefit from specifying the particular application or industry to which it applies. This article will now explore [briefly state the topics the article will cover, e.g., the advantages of high-temperature electrical systems in aerospace, or the materials used in producing these critical components].
electra hot
Understanding the essential aspects of "electra hot" is crucial for appreciating its role in various applications. These key aspects encompass design, material science, and performance considerations.
- High temperature
- Electrical conductivity
- Material properties
- System design
- Safety protocols
- Thermal management
- Performance testing
- Applications (e.g., aerospace)
These eight aspects interconnect intricately. High-temperature operation necessitates specialized materials with excellent electrical conductivity and thermal stability. Rigorous system design and safety protocols are essential. Performance testing ensures components meet intended operational parameters. Thermal management becomes vital for prolonged high-temperature use. Examples of applications include high-performance electrical systems in aerospace, where components must withstand intense heat and maintain conductivity to function reliably.
1. High Temperature
High temperature is a defining characteristic of "electra hot" systems. The ability to operate at elevated temperatures is crucial for performance in various applications. This necessitates specific material selection and design considerations. Materials must possess exceptional thermal stability and electrical conductivity to withstand the intense heat without degrading performance. Examples include specialized high-temperature alloys and ceramics used in aerospace and industrial applications requiring sustained high-temperature operation. The inherent link between operating temperature and component performance is paramount. High-temperature operation directly affects the component's lifespan and efficiency.
The practical significance of understanding this connection lies in the ability to predict and mitigate potential failures. Detailed analysis of material properties and thermal characteristics are crucial for ensuring reliable operation under demanding conditions. Failure to account for high temperatures can result in premature component degradation, system malfunctions, and potential safety hazards. Understanding how temperature influences the electrical and physical properties of components is paramount for optimal design and engineering solutions. Successful implementation of "electra hot" solutions requires meticulous consideration of the high-temperature operating environment.
In summary, high temperature is an integral component of "electra hot" systems. The ability to maintain operational performance under extreme temperatures necessitates precise material selection, careful design, and comprehensive testing. Understanding the interplay between temperature and component performance is crucial for successful design and the development of reliable, high-performance systems.
2. Electrical Conductivity
Electrical conductivity is a fundamental property directly impacting the performance and reliability of "electra hot" systems. High-temperature operation often necessitates materials capable of maintaining electrical conductivity under extreme conditions. This characteristic is vital for efficient energy transfer and reliable operation, particularly in demanding applications like aerospace and industrial processes.
- Material Selection and Design
The choice of materials is critical. Materials with high conductivity at elevated temperatures are essential for maintaining efficient power transmission. This necessitates careful consideration of factors like thermal expansion, oxidation resistance, and chemical compatibility with other system components. Examples include specific metallic alloys designed for high-temperature applications, like nickel-based superalloys, or high-temperature ceramic materials exhibiting exceptional electrical conductivity. These materials must meet specific conductivity requirements in high-temperature settings to avoid significant performance loss or failure.
- Impact on System Performance
Decreased conductivity at elevated temperatures can lead to significant performance degradation in "electra hot" systems. This manifests as increased resistance, reduced current flow, and potentially higher energy consumption. Reduced power efficiency directly impacts system efficacy and overall cost. The maintenance of conductivity, particularly under extreme temperature conditions, is paramount for consistent and reliable power delivery.
- Role in Safety Considerations
The maintenance of electrical conductivity is vital for safety. A system's ability to maintain appropriate conductivity directly affects the prevention of electrical arcing and short circuits. In high-temperature environments, any reduction in conductivity could lead to localized overheating, potentially causing damage to components and posing safety risks. Designing components and systems with reliable conductivity under high-temperature conditions is crucial for preventing catastrophic failure.
- Testing and Verification
Thorough testing procedures, encompassing a wide range of temperatures and operational parameters, are essential. These assessments are critical to ascertain the sustained conductivity of materials under high-temperature stresses. These tests help predict the operational lifetime of the "electra hot" system in anticipated real-world conditions. Data acquired in these testing phases provides critical insights into the limits of performance and operational tolerances, supporting system design optimization and refinement.
In conclusion, the interplay between electrical conductivity and "electra hot" systems is paramount. Careful consideration of material properties, system design, safety procedures, and testing protocols are all critical to achieving optimal performance, safety, and longevity in high-temperature, high-conductivity applications.
3. Material Properties
Material properties are foundational to the functionality and reliability of "electra hot" systems. The selection of materials directly impacts a system's ability to withstand high temperatures, maintain electrical conductivity, and prevent degradation during operation. The specific properties required vary greatly depending on the intended application.
For instance, in aerospace applications where "electra hot" components experience extreme thermal fluctuations, materials must possess excellent thermal stability. High-temperature alloys like nickel-based superalloys, known for their strength and resistance to oxidation at elevated temperatures, are common choices. Similarly, in industrial processes, materials resistant to chemical corrosion and degradation under high temperatures are critical. The suitability of a material depends heavily on its thermal conductivity, its resistance to creep (deformation under sustained stress), and its resistance to oxidation or other degradation mechanisms. In summary, the selection process prioritizes materials capable of preserving their desired properties under extreme heat.
Understanding the interplay between material properties and high-temperature performance is essential for design engineers. A thorough analysis of tensile strength, thermal expansion, and specific heat capacity is crucial. Failure to account for these properties can lead to material failure, component degradation, and ultimately, system malfunction. Real-world examples demonstrate the critical importance of choosing appropriate materials. Failures in early jet engine designs stemmed from inadequate material selection, highlighting the dire consequences of overlooking material science principles in high-temperature applications. Proper selection and utilization of materials directly translate to the reliable and efficient operation of "electra hot" systems. The choice of appropriate materials, guided by a deep understanding of material properties, leads to high-performance, long-lasting solutions.
4. System design
System design is integral to the success of "electra hot" systems. Effective design directly influences a system's ability to operate reliably at elevated temperatures. This involves careful consideration of factors like thermal management, material selection, and safety protocols. A poorly designed system, even with excellent materials, may fail prematurely due to inadequate heat dissipation, stress concentrations, or flawed safety mechanisms. Conversely, a well-designed system can maximize the lifespan and efficiency of "electra hot" components. The design process must anticipate and address potential issues stemming from the extreme operating conditions.
Real-world examples underscore the importance of sound system design. Early jet engine designs often failed due to insufficient thermal management, highlighting how a poorly conceived system can lead to rapid component degradation. Modern designs incorporate advanced cooling systems, carefully engineered heat sinks, and strategically placed insulation to maintain optimal operating temperatures. These meticulous design choices ensure reliable performance under demanding conditions. Similarly, in industrial high-temperature processes, the system architecture profoundly affects the longevity and efficiency of the overall operation. The design must account for the dynamic thermal environment, safeguarding against overheating and ensuring consistent performance over the system's lifespan.
The practical significance of understanding the connection between system design and "electra hot" systems is substantial. By incorporating robust thermal management strategies, engineers can extend the operational life of components, minimize downtime, and reduce maintenance costs. A thorough design process that meticulously addresses the unique challenges of high-temperature operation directly translates to improved reliability and efficiency in various industries. Failure to consider these design principles leads to costly failures, potential safety hazards, and decreased system availability. In conclusion, sound system design is not just a technical aspect but a fundamental prerequisite for the dependable and cost-effective operation of any "electra hot" system.
5. Safety Protocols
Safety protocols are paramount in the operation of "electra hot" systems. The inherent high temperatures and associated electrical components present inherent risks. Effective safety protocols are critical to mitigating these dangers and ensuring the safe operation of these systems. Failure to adhere to these protocols can lead to significant consequences, ranging from equipment damage to severe injury or environmental damage. Consequently, meticulous attention to safety protocols is indispensable.
- Insulation and Enclosure Design
Proper insulation and enclosure design is crucial. Materials selected must withstand the extreme temperatures and prevent electrical arcing or short circuits. Effective insulation reduces the risk of heat transfer and reduces the possibility of burns or fires. Improper insulation can lead to overheating of adjacent materials, potentially causing structural failures or fires. Specific materials, carefully engineered, and designed for high-temperature applications are necessary. Robust and well-sealed enclosures protect personnel and the surrounding environment from hazardous elements. Real-world examples include the precise insulation used in high-temperature electrical connectors and the robust casing surrounding high-power electrical transformers.
- Overcurrent Protection and Circuit Breakers
Effective overcurrent protection mechanisms, such as circuit breakers, are essential. These systems rapidly interrupt current flow if the system experiences a surge or short circuit. This prevents overheating and potential fires. Proper sizing and calibration of circuit breakers are critical. Inadequate protection can lead to component damage, fires, or even explosions. Properly designed and integrated overcurrent protection is crucial for the reliability and safety of "electra hot" systems. A vital application of this principle is found in the design of electrical systems for furnaces and other industrial high-temperature equipment.
- Emergency Shutdown Systems
Robust emergency shutdown systems are critical for rapid intervention in case of unforeseen events. These systems allow for immediate cessation of operation during emergencies, preventing further damage or injury. Failure of these systems can lead to escalating issues, including equipment damage and potential hazardous events. Redundancy in shutdown mechanisms improves the likelihood of successful intervention. These systems are crucial in safeguarding human life and mitigating potential environmental hazards.
- Personnel Training and Protocols
Comprehensive training for personnel operating and maintaining "electra hot" systems is essential. Appropriate safety training equips personnel to recognize potential hazards and take appropriate action in case of emergencies. This also includes familiarity with safety procedures, emergency protocols, and handling of potential equipment malfunctions. Specific procedures related to entry into or working around "electra hot" equipment must be meticulously followed. Compliance with safety protocols and procedures by personnel is critical to ensuring operational safety and minimizing risks.
In summary, robust safety protocols are not merely add-ons but are integral components of any "electra hot" system. Implementing these protocols minimizes risks, protects personnel, and ensures system reliability and longevity. The integration of these elements into the design and operational phases of "electra hot" projects fundamentally addresses the safety risks of high-temperature electrical systems. This emphasis on safety is not merely prudent but necessary for the successful and sustainable operation of these systems in various industries.
6. Thermal Management
Effective thermal management is critical for the reliable and efficient operation of "electra hot" systems. Maintaining desired temperatures is essential to prevent component degradation, ensure consistent electrical conductivity, and maintain system safety. Failure to adequately manage heat generation and dissipation can lead to performance limitations, premature failure, and potential safety hazards. The criticality of thermal management in high-temperature applications cannot be overstated.
- Heat Generation and Dispersion Mechanisms
Understanding the precise mechanisms of heat generation within the system is paramount. This includes considering the electrical resistance of components, the resistive heating effect, and the presence of other energy conversion processes. Equally crucial is the design of effective heat dispersion mechanisms. This involves employing appropriate cooling methods, like forced air cooling, liquid cooling, or advanced thermal management solutions such as phase-change materials or heat pipes. The interplay between heat generation and dissipation directly affects the system's operational temperature, longevity, and overall performance.
- Material Selection and Design
Material selection directly impacts the ability of a system to manage heat. Materials with high thermal conductivity and appropriate melting points are crucial to dissipate heat efficiently. System design must optimize heat transfer paths and prevent localized overheating. This often requires innovative designs that incorporate efficient heat sinks, thermal insulators, and precise component placement. These design considerations must effectively balance operational requirements with temperature constraints.
- Thermal Testing and Modeling
Comprehensive thermal testing and modeling are essential to validate the design's efficacy. Predictive models help anticipate thermal behavior under varying operating conditions and identify potential weaknesses. Testing should encompass a range of operating temperatures and environmental factors. Failure to incorporate rigorous thermal testing can lead to unforeseen failures under real-world conditions, potentially leading to operational problems. Thorough modeling and experimental verification provide vital insights into the limitations and potential risks of high-temperature systems.
- Impact on Component Longevity
Effective thermal management directly impacts the longevity of components. Excessive heat leads to accelerated degradation and failure. Precise control of temperature distribution ensures components operate within their safe operating parameters, maximizing their lifespan and reliability. This results in a system capable of continuous, reliable operation in high-temperature applications. Proper thermal management reduces the frequency of component replacements and repairs, minimizing operational costs.
In summary, thermal management is inextricably linked to the success of "electra hot" systems. Precise understanding of heat generation, selection of suitable materials, meticulous design, and comprehensive testing are critical components for creating robust and dependable systems. Effective thermal management directly impacts the longevity, performance, and safety of high-temperature electrical systems, making it an essential design consideration.
7. Performance testing
Performance testing is an indispensable component of "electra hot" system development. It assesses the system's ability to maintain intended performance under extreme temperature conditions. The validity of the system's design, material selection, and thermal management strategies are scrutinized through rigorous testing protocols. Failure to conduct comprehensive performance testing can lead to unforeseen issues, system failures, and potential safety hazards. Real-world examples demonstrate the consequences of neglecting these crucial tests. Early jet engine designs, lacking sufficient testing procedures for high-temperature operation, frequently experienced catastrophic failures.
Testing protocols typically involve subjecting components and systems to various temperature profiles, simulating expected operational conditions. Measurements of electrical conductivity, thermal stability, and component integrity are crucial outputs. Data analysis identifies potential weaknesses and areas for improvement in the design or materials. For instance, simulations and experiments might analyze the behavior of high-temperature alloys under prolonged thermal stresses, determining their structural integrity and electrical conductivity at different operating temperatures. These tests provide quantitative data, enabling engineers to make informed decisions regarding material selection, system design modifications, and operational parameters. A precise understanding of how electrical conductivity varies with temperature is essential. Similarly, testing helps identify the threshold at which materials begin to degrade or exhibit undesirable characteristics.
The practical significance of this rigorous approach is evident in the development of reliable high-temperature systems. By identifying potential issues and vulnerabilities during the testing phase, manufacturers mitigate risks associated with system failures during operational deployment. This reduces costly repairs, operational disruptions, and potential safety incidents. In conclusion, performance testing provides a crucial link between theoretical design and actual system performance, underscoring its vital role in the development and implementation of "electra hot" technologies.
8. Applications (e.g., aerospace)
The application of "electra hot" principles in aerospace engineering is critical for developing high-performance systems. Components must withstand extreme temperatures and maintain optimal electrical conductivity to ensure reliable operation under demanding conditions. These applications require a sophisticated understanding of materials science and engineering to meet stringent performance and safety requirements.
- High-Temperature Electrical Systems
Aerospace vehicles often operate in environments with substantial temperature fluctuations. Reliable electrical systems are essential for navigation, communication, and control functions. "Electra hot" systems are crucial for power generation and distribution, enabling the operation of sensitive instruments and equipment under extreme thermal conditions. Examples include electrical systems in jet engines and advanced propulsion systems, where components must maintain functionality at high temperatures generated by combustion.
- Advanced Propulsion Systems
Advanced propulsion systems, such as those found in spacecraft and high-performance aircraft, necessitate components capable of functioning reliably in intense heat. High-temperature electrical systems are fundamental to ignition, control, and operation of these complex systems. Components in these systems may face extreme temperatures from combustion, friction, or aerodynamic forces. Effective thermal management is crucial to ensuring the longevity and safety of these components.
- Materials Science and Engineering
The development of "electra hot" systems hinges on specialized materials science and engineering. Materials need to withstand extreme temperatures without compromising structural integrity or electrical conductivity. This demands research into and development of high-temperature alloys, advanced ceramics, and other specialized materials. For example, the development of specific superalloys with exceptional high-temperature strength and oxidation resistance is critical for jet engine components. The need for such materials drives innovative approaches in materials science and engineering.
- Safety and Reliability Considerations
In aerospace applications, safety and reliability are paramount. "Electra hot" systems must be designed and tested to operate reliably and safely under the rigorous conditions of flight. Safety protocols, such as redundancy in critical systems and comprehensive testing, are critical. For example, in aircraft engines, the electrical system must withstand extreme temperatures and pressures without failure. This necessitates careful design considerations and robust safety measures to prevent malfunctions and safeguard against accidents.
In conclusion, "electra hot" technologies are not just a theoretical concept in aerospace engineering; they are vital for the development of reliable, high-performance systems. The application of these principles drives advancements in materials science, ensures safety, and directly contributes to the efficiency and performance of aircraft, spacecraft, and other aerospace vehicles. The demands of these applications highlight the continuous need for innovation and research in high-temperature electrical engineering.
Frequently Asked Questions about "Electra Hot"
This section addresses common inquiries regarding "Electra Hot" systems, providing concise and informative answers. The information presented is based on established principles in materials science, electrical engineering, and related disciplines.
Question 1: What does "Electra Hot" signify in the context of electrical systems?
The term "Electra Hot" likely designates a component or system designed to operate reliably at elevated temperatures. This implies specialized materials and designs crucial for maintaining electrical conductivity and structural integrity under extreme heat. The specific meaning will depend on the industry or application.
Question 2: What are the key materials considerations for "Electra Hot" systems?
Materials employed in "Electra Hot" systems must exhibit exceptional thermal stability, high electrical conductivity, and resistance to degradation at elevated temperatures. Common choices include high-temperature alloys and advanced ceramics.
Question 3: How does thermal management impact "Electra Hot" system performance?
Effective thermal management is crucial. Strategies for dissipating generated heat, such as cooling systems and careful material selection, are vital. Inadequate thermal management can lead to component failure due to overheating.
Question 4: What safety protocols are essential for "Electra Hot" systems?
Safety is paramount. Robust insulation, enclosed designs, overcurrent protection, and emergency shutdown systems are crucial components. These protocols mitigate the risks associated with elevated temperatures and electrical currents.
Question 5: What are the typical applications for "Electra Hot" technology?
Applications span various sectors. Aerospace, particularly in jet engines and propulsion systems, often employs "Electra Hot" components due to extreme operating temperatures. High-temperature industrial processes also utilize these systems.
Question 6: What are the potential consequences of neglecting proper design and testing for "Electra Hot" systems?
Neglecting rigorous design and testing can result in system failures, reduced lifespan of components, increased maintenance costs, and potential safety hazards. Thorough testing and analysis are vital to ensure reliability and safety under demanding conditions.
In summary, understanding the principles behind "Electra Hot" systems is crucial for reliable operation and safety. This requires careful attention to material selection, thermal management, safety protocols, and rigorous testing.
The following sections will delve into the specific design and application aspects of "Electra Hot" systems in greater detail.
Tips for Designing and Implementing "Electra Hot" Systems
Effective design and implementation of "Electra Hot" systems hinge on meticulous attention to detail. These tips provide guidance for engineers and designers working with high-temperature electrical components and systems.
Tip 1: Prioritize Material Selection.
Appropriate material selection is paramount. Materials must exhibit exceptional thermal stability, high electrical conductivity, and resistance to degradation at elevated temperatures. Consider factors like thermal expansion, creep resistance, and oxidation resistance. Specific high-temperature alloys and advanced ceramics are often crucial. Examples include nickel-based superalloys for aerospace applications and specialized ceramics for high-voltage insulation.
Tip 2: Optimize Thermal Management.
Effective heat dissipation is critical. Design should incorporate efficient cooling mechanisms, such as forced air or liquid cooling. Careful consideration of heat transfer pathways is essential. Utilize materials with high thermal conductivity and minimize thermal stresses by employing insulation and heat sinks strategically.
Tip 3: Implement Robust Safety Protocols.
Safety is paramount. Designs must incorporate redundancy and multiple safeguards against potential failures. Implement robust insulation materials, use enclosed designs for components, and employ overcurrent protection devices. Ensure emergency shutdown systems are readily available and tested regularly. Adhering to industry safety standards is mandatory.
Tip 4: Rigorous Performance Testing.
Extensive testing is crucial to ensure reliability. Systems should undergo rigorous thermal and electrical testing under various operating conditions, including anticipated peak loads. Employ simulation and modeling techniques to evaluate performance parameters under extreme conditions. Analysis should be thorough and systematic, considering potential failure modes.
Tip 5: Employ Redundancy and Fail-Safes.
Redundancy in critical components and fail-safe mechanisms enhance system reliability. This reduces the likelihood of catastrophic failure in case of component malfunction. Duplication of critical circuits and backup systems are essential to maintain functionality in the event of component failure. This ensures continuous operation under demanding circumstances.
Tip 6: Adhere to Industry Standards and Regulations.
Compliance with relevant industry standards and regulations is mandatory. Consult relevant codes and regulations for appropriate design and testing procedures. Strict adherence to safety and quality control standards guarantees safe and reliable operation.
Following these tips allows for the development of reliable and high-performing "Electra Hot" systems while mitigating risks. These strategies lead to enhanced safety, improved efficiency, and extended lifespan of these critical components and systems.
The next section will explore the detailed design considerations for specific "Electra Hot" applications, such as in aerospace and industrial processes.
Conclusion
This article explored the multifaceted nature of "Electra Hot" systems, emphasizing the critical interplay between materials science, thermal management, safety protocols, and performance testing. The analysis highlighted the importance of meticulous design choices for achieving reliable operation under extreme thermal conditions. Key considerations included the selection of materials capable of sustaining high temperatures without compromising electrical conductivity, the implementation of effective cooling mechanisms to control temperature distribution, the incorporation of robust safety protocols to mitigate risks, and the rigorous testing procedures necessary for verification of performance under operational stresses. Furthermore, the article underscored the significance of "Electra Hot" technology in diverse applications, particularly in aerospace and industrial processes.
The ongoing quest for enhanced performance and reliability in high-temperature environments necessitates continued research and development in "Electra Hot" technologies. The future of these systems hinges on breakthroughs in material science, advanced thermal management techniques, and innovative system designs. Addressing the challenges presented by extreme operating conditions will be critical for advancements in various sectors, ensuring sustained high-performance capabilities under demanding conditions. Continued adherence to rigorous design principles, coupled with thorough testing procedures and stringent safety protocols, is essential for the safe and reliable deployment of these systems in the future.
You Might Also Like
Everything About Kuch: Your GuideA&W Root Beer Ownership: Who Owns The Iconic Brand?
David McCallum Age: How Old Is The Legendary Actor?
Josh Altman Salary: 2023 Earnings Revealed!
Best Doc Spartan Reviews & Expert Opinions
Article Recommendations


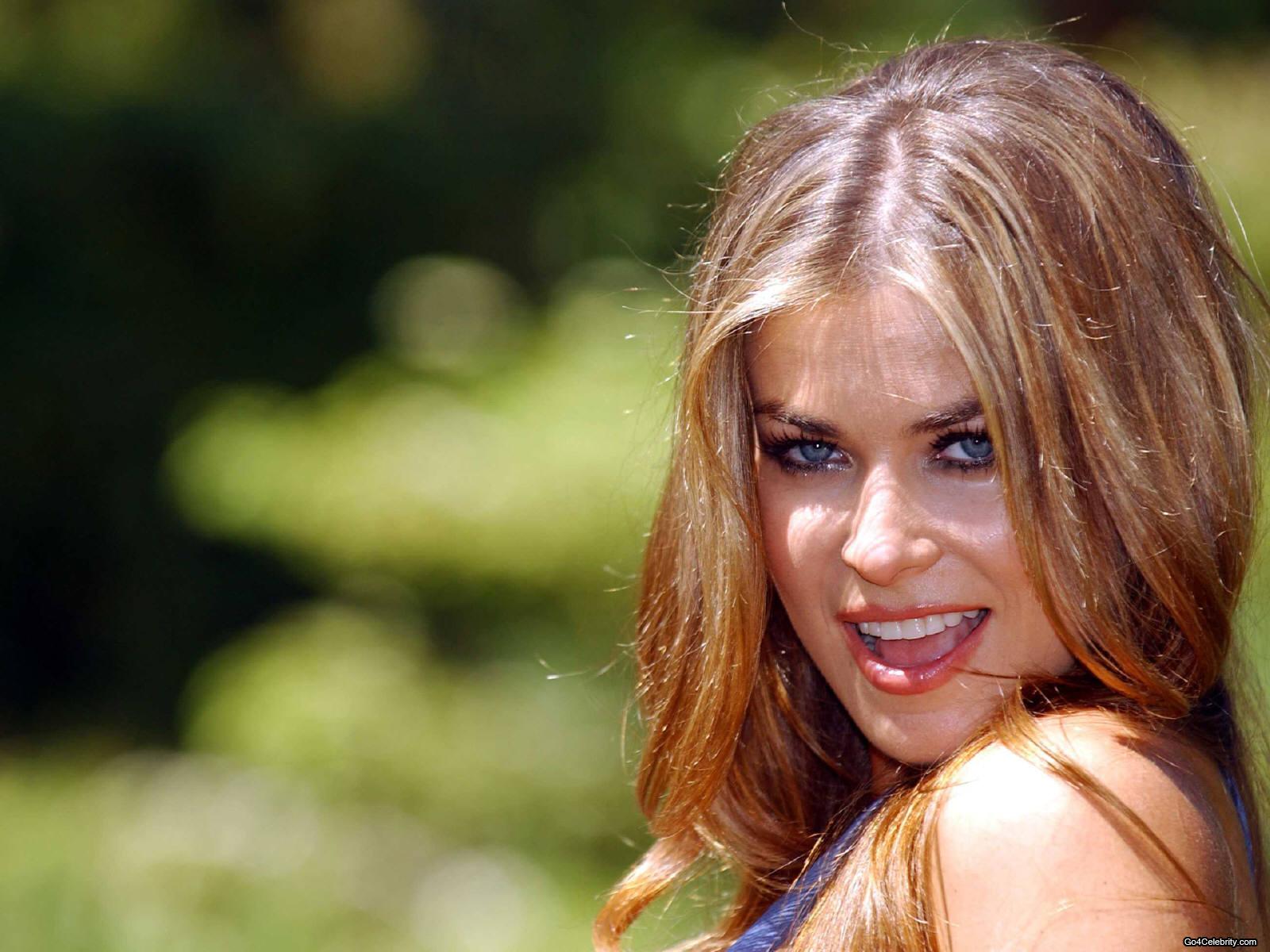